| April 30, 2025
Lamination is an essential process in packaging and logistics, enhancing both the functional and aesthetic properties of materials. This technique involves bonding different layers of foam—varying in color, density, and thickness—or multiple layers of the same foam to create composite products with improved performance.
Among the various techniques available, heat lamination has emerged as one of the most efficient and cost-effective options. At Worldwide Foam, we proudly offer heat lamination services in Mexico.
Thanks to this technology, permanent bonding can be achieved without the need for chemical adhesives. In this blog, we explain how heat lamination works and highlight the key benefits it brings to your manufacturing process.
What is heat lamination?
Heat lamination involves heating the surface of a foam material until it softens and becomes tacky. By pressing two surfaces together, this molten layer acts as a natural adhesive, forming a strong, durable bond.
This process eliminates the need for additional glues or chemicals, improving the purity of the final product and reducing costs. It also enables the combination of different foam types, colors, and densities to create custom laminates tailored to specific customer needs.
The lamination process: how it works
At Worldwide Foam, our heat lamination process includes the following steps.
Material preparation
The layers to be bonded are selected—these may include foams of varying densities or combinations with other technical materials.
Heat application
A heated blade or roller is used to melt the surface of the foam.
Controlled pressure
The heated surfaces are pressed together, forming a permanent bond.
Cooling and stabilization
The laminate is cooled and stabilized to ensure consistency and product quality. Thanks to precise control of temperature and pressure, the result is a homogeneous bond—free of bubbles or defects—with a smooth appearance and improved strength.
Key benefits of heat lamination
Heat lamination offers numerous advantages for manufacturers in packaging, logistics, and other industries. Here are the top benefits.
Strong, clean material bond
Since no adhesives are used, the bond between layers is cleaner and more reliable. This reduces the risk of delamination, especially in applications requiring long-term performance.
Enhanced durability
Thermal bonding improves the structural integrity of the final product. Laminated foams exhibit greater resistance to wear, compression, moisture, and impact—making them ideal for demanding industrial uses.
Higher production efficiency
The automated nature of heat lamination shortens production time by eliminating extra steps like gluing, drying, or curing. This translates into lower energy usage and faster turnaround.
Design versatility
This technology allows for the combination of different materials to meet specific needs. Multi-layer foams can be designed with properties such as thermal insulation, impact absorption, or vibration dampening.
Cost-effective
Without adhesives, heat lamination reduces waste and eliminates emissions of volatile organic compounds (VOCs). It’s also more efficient, helping to cut operating costs.
Common applications of heat lamination
Heat lamination is widely used across various industries, including:
Automotive: insulation panels, seals, gaskets, and interior components
Electronics: protection for sensitive components and anti-static packaging
Construction: thermal and acoustic insulation for walls and ceilings
Industrial Packaging: reinforced protection for fragile or high-value items
Sports & Healthcare: helmet liners, insoles, and protective gear
Worldwide Foam lamination: precision and quality
Our lamination services are tailored to meet each customer’s technical requirements. We work with a wide range of materials and foams, including:
CROSSLINK XLPE: closed-cell, water-resistant, thermoformable foam
XLPE CHEMICALLY CROSSLINK ROLLS: with a large cell structure and excellent conformability
XLPE IRRADIATED SERIES ROLLS: smooth surface and uniform density
WZ302 (Zotefoams Azote Series): low-VOC foams ideal for specialized applications
Elastomeric Foam: versatile solutions for a variety of industries
With our experience and cutting-edge technology, we guarantee high-quality lamination capable of meeting even the most demanding specifications. Heat lamination is a smart, efficient, and environmentally friendly method for manufacturing high-performance foam products.
Its advantages in material bonding, durability, and operational efficiency make it the ideal choice for companies looking to optimize production and deliver long-lasting, high-quality products. At Worldwide Foam, we have the infrastructure and expertise to elevate your projects with the latest in lamination technology.
Contact us today to learn more about our solutions—and turn your ideas into outstanding products.
Worldwide Foam
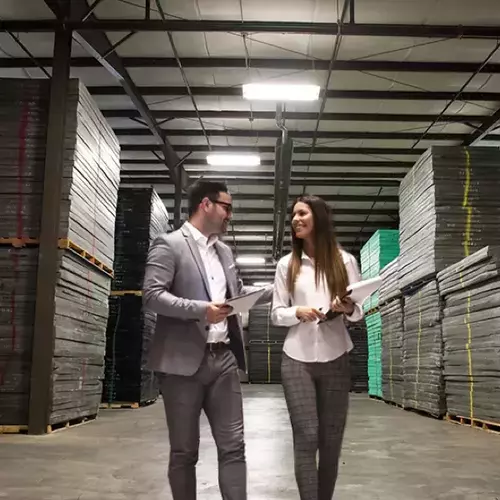
We are leaders in the supply of closed cell polyethylene foam in Mexico. We support various industries by offering a wide range of products and complementary services.