| August 28, 2024
Polyethylene foam is a versatile material that can enhance various products and services, and one of the most effective ways to do so is through heat lamination. In this article, we will explain what heat lamination of polyethylene foam is and the advantages it offers.
What is heat lamination of polyethylene foam?
Heat lamination of polyethylene foam is a process where high temperatures are used to fuse layers of polyethylene foam together. This involves passing the materials through a heated blade, which melts the foam's surface, turning it into a sticky substance that acts as a natural adhesive.
This technique allows for the creation of multi-layer composite sheets by combining different materials, densities, and colors, resulting in customized, high-quality products. Worldwide Foam, an industry leader, offers lamination services in several strategic locations, including Elkhart, Indiana; Atlanta, Georgia; Ontario, California; and Silao, Mexico.
These facilities are equipped with state-of-the-art technology to ensure an efficient and effective lamination process.
Advantages of heat lamination of polyethylene foam
Lamination is a crucial technique in the materials industry, particularly for polyethylene foam. Heat lamination has gained popularity due to its numerous advantages, especially in creating high-quality, durable products.
Permanent and durable bonding
One of the main advantages of heat lamination is the creation of a permanent bond. The heat melts the surface of the polyethylene foam, allowing the layers to fuse together in a solid and durable manner. This process eliminates the need for additional adhesives, reducing costs and improving efficiency. Increased strength and stability By fusing the polyethylene foam layers together with heat, the final product achieves greater strength and stability. This is particularly important in applications where the material must withstand heavy loads or have extended durability.
Increased strength and stability
By fusing the polyethylene foam layers together using heat, greater strength and stability is achieved in the final product. This is especially important in applications where the material is required to withstand loads or have extended durability.
Versatility in the combination of materials
Heat lamination allows different types of materials and densities to be combined into a single composite sheet. This provides great flexibility in the design and manufacture of customized products. For example, sheets can be created with specific properties such as water resistance, thermal insulation, or acoustic insulation, depending on the customer's needs.
Efficiency and cost-effectiveness
This process is more cost-effective compared to using traditional adhesives. The elimination of adhesives not only reduces production costs but also simplifies the manufacturing process, leading to higher efficiency and shorter production times.
Improved product performance
Heat lamination enhances overall product performance. By eliminating the need for adhesives, it prevents material degradation over time, resulting in higher-quality, longer-lasting products.
Diverse applications
Heat-laminated products have a wide range of applications across various industries. From construction and automotive to packaging, polyethylene foam heat lamination provides efficient and high-quality solutions.
Applications and uses in various industries
The versatility of polyethylene foam heat lamination allows for its use in multiple applications. In the construction industry, for example, it is used to create thermal and acoustic insulation panels, as well as filler materials for structures.
In the automotive sector, it is used in the production of components that require high strength and durability. Additionally, in the packaging industry, heat-laminated polyethylene foam offers lightweight and robust solutions for product protection.
Worldwide Foam’s facilities in Elkhart, Indiana; Atlanta, Georgia; Ontario, California; and Silao, Mexico, are strategically located to serve customers in various regions, ensuring fast and efficient service. These locations enable the company to offer customized solutions tailored to each customer's specific needs.
Heat lamination of polyethylene foam is a process that offers numerous advantages in terms of durability, strength, and efficiency. By fusing the foam layers together using heat, a permanent, high-quality bond is achieved, resulting in superior, higher-performing products.
Worldwide Foam, with its state-of-the-art facilities in Elkhart, Indiana; Atlanta, Georgia; Ontario, California; and Silao, Mexico, positions itself as an industry leader, providing innovative and customized solutions to meet its customers' needs.
In summary, heat lamination is a technique that not only improves the quality of polyethylene foam but also optimizes production processes, making them more cost-effective and efficient. The ability to combine different materials and densities allows for the creation of unique products tailored to a wide range of applications, solidifying Worldwide Foam as a leader in the sector.
Worldwide Foam
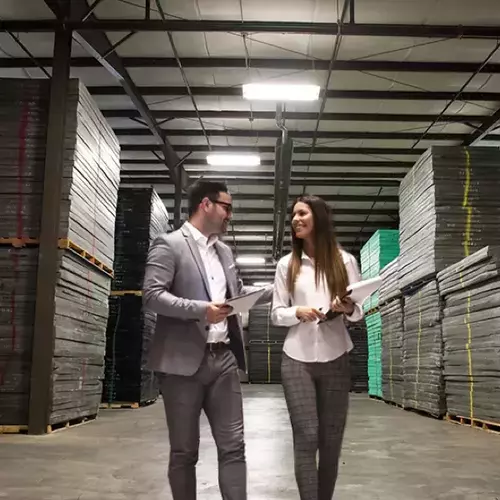
We are leaders in the supply of closed cell polyethylene foam in Mexico. We support various industries by offering a wide range of products and complementary services.